Digital Transformation – Manufacturing
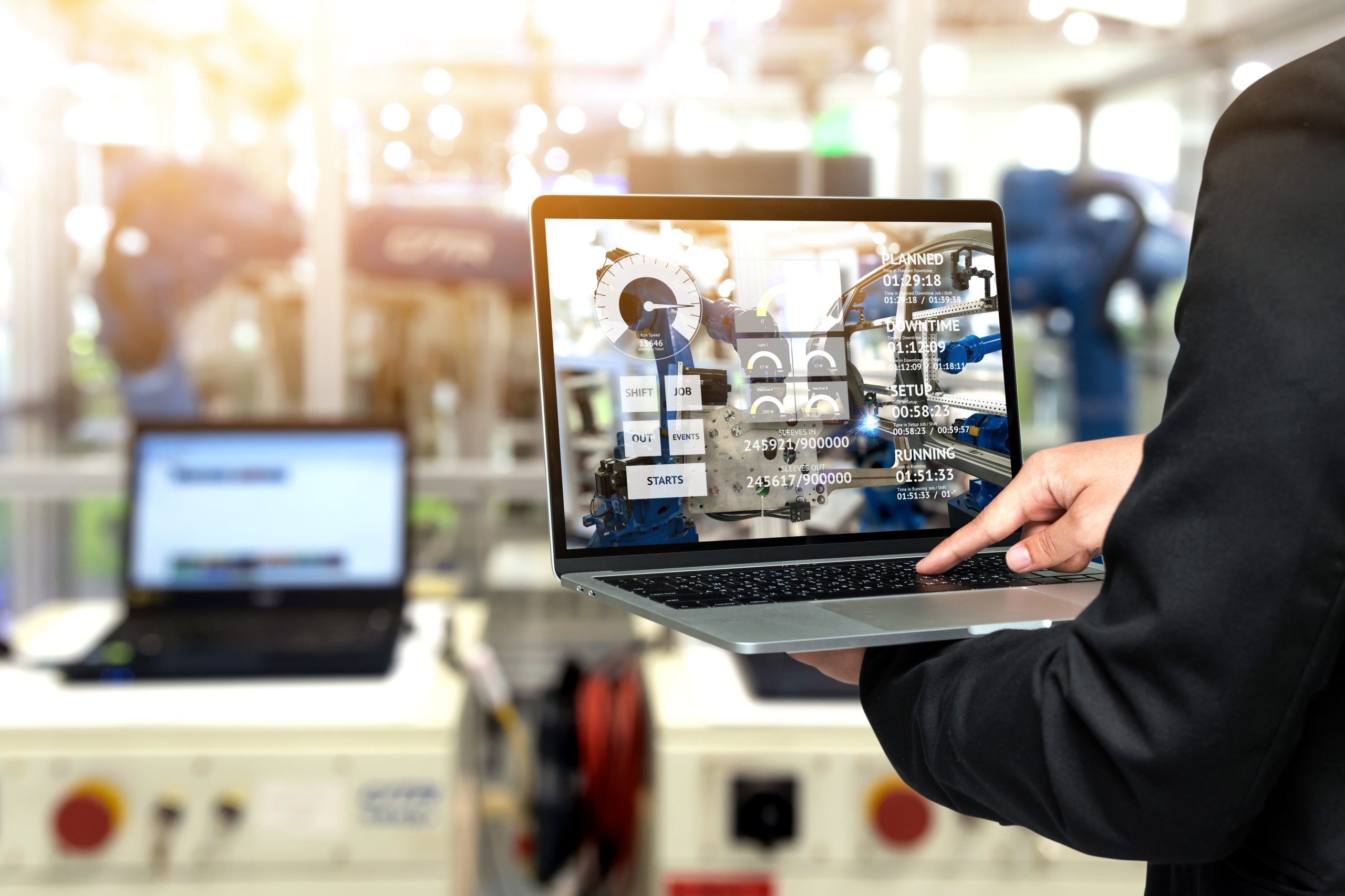
Digital Transformation in the Chemical and Manufacturing Industry
Background: A global provider of treated wood products, wood treatment chemicals, and carbon compounds, headquartered in Pittsburgh, Pennsylvania, embarked on a comprehensive digital transformation initiative. The company’s products and services are used in various niche applications across diverse end-markets, including the railroad, specialty chemical, utility, residential lumber, agriculture, aluminum, steel, rubber, and construction industries. With over 1,800 employees, the company serves its customers through a comprehensive global manufacturing and distribution network, with facilities located in North America, South America, Australia, China, and Europe.
Challenge: The company faced increasing pressure to stay attuned to the latest technology trends and use best-of-breed cloud software platforms to optimize its organizational business needs efficiently and effectively. There was a lack of formal process or structure to request any app or reporting needs, leading to critical requests often getting buried in email correspondence, excel sheets, or stand-alone reports. Primary challenges included ease of data access and data mapping, especially for cross-functional teams.
Solution: The company partnered with All Lines Technology to develop and implement a Digital Transformation strategy. The goal was to create a strategy and plan that could be scaled up and rolled out to the entire organization. The company and its partner started working on these challenges and potential solutions. After many discussions and whiteboarding sessions, the core team was formed. The core team followed a recommended 7-step approach for Digital Transformation strategy and came up with a solution to build a “Common Data Platform” – a data platform powered by Microsoft technology stack, including Power Platform and Microsoft Azure, which would serve as a common source of truth for all reporting and AppDev needs. Using native ETL and Application Development facilities in Azure technology stack, the Digital Transformation journey’s technology portion was streamlined perfectly.
Results: During the first 12 months since the inception of the Digital Transformation initiative, the company saw more than 30 initiatives introduced and implemented. The Digital Transformation core team is still going strong, with thousands of users using a multitude of apps for various functions. From tracking and managing rail car loading/unloading, managing secret recipes for super-secret formulas, to celebrating and capturing social outreach moments with co-workers.
Benefits: The benefits of this digital transformation project include:
- Improved Data Access and Mapping: The Common Data Platform provides a centralized source of truth, making it easier for cross-functional teams to access and map data efficiently.
- Enhanced Employee Engagement: The seamless integration of Microsoft products enabled quick turnaround for app development and opened endless possibilities for integrated solutions across various departments and business units.
- Increased Efficiency: The streamlined technology portion of the Digital Transformation journey allowed for the introduction and implementation of over 30 initiatives within the first 12 months.
Scalability: The strategy and plan developed can be scaled up and rolled out to the entire organization, ensuring long-term success and adaptability.
Client Satisfaction
These advancements not only optimized operational processes but also ensured a more responsive and agile environment, ultimately leading to higher efficiency and higher trust in the company’s capabilities.